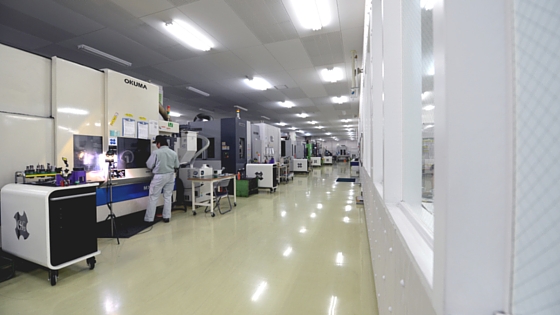
1. Manufacturing jobs are low income jobs.
On average, manufacturing workers earn $77,060 yearly while other average workers earn $60,168. According to Anthony Carnevale, director of the Georgetown University Center on Education and the Workforce, 20% of workers with technical certificates earn more than the workers with Bachelor’s of Arts degrees. 30% of workers with associate’s degrees make more than the workers with four-year college degrees. Even 20 years after graduation this stays true.
2. Manufacturing jobs are blue-collar and low skilled jobs, so they are only for “certain” people.
Manufacturing jobs require creativity, innovation, analytical and problem solving skills. You will be surprised to see how challenging and high tech manufacturing jobs can be especially when you get involved in R&D. According to the Manufacturing Institute, 80% of manufactures are experiencing a skills gap. Their applicants are not skilled enough to perform in production positions that require high levels of critical thinking. The majority of manufacturers help their employees pursue higher education while they work by providing financial help.
3. Manufacturing jobs are dirty jobs with oily floors and noisy machines.
Nowadays, manufacturing has also turned into a high-tech industry. Machines look very modern, and are operated with computers and touch screen key boards. Shop floors are clean and shop temperature is controlled to maintain product quality. The days of the dirty floors and miserable shop conditions are a thing of the past!
On the first Friday in October annually, MFG DAY leads the way to inspire future manufacturers. Its missions include addressing stigmas of manufacturing by encouraging current manufacturers to show what the modern manufacturing really is like. Many manufactures joined its effort and held numerous events this year to invite students from high schools or technical colleges. According to a post-event survey conducted by MFG DAY, as a result of their efforts and collaboration with manufacturers, 81% of students believe that manufacturing jobs are both interesting and rewarding, and 71% of students want to tell their friends and families about manufacturing. By motivating and educating students, we are shaping the future of manufacturing!
Sources:
http://www.mfgcareers.org/mfg/parent.asp
http://www.themanufacturinginstitute.org/
http://techcrunch.com/2015/11/15/stem-education-meet-the-new-manufacturing/